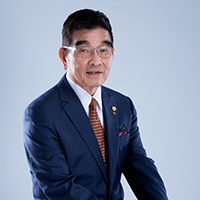
Chairman  Mr. B. F. Hsu
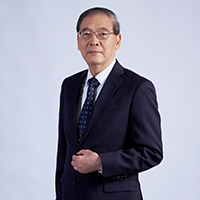
Vice Chairman  Mr. S. S. Hsu
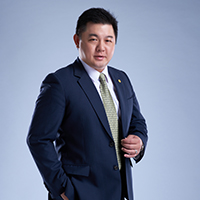
President  Mr. I. T. Hsu
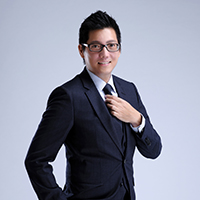
CEO  Mr. I. S. Hsu
Our company was founded with the aspiration of establishing a Chinese enterprise that could stand firm on the international stage. We built our factory in Tucheng Township, Taipei County, with the goal of developing heavy electrical machinery products, contributing to society, enhancing employee welfare, and sharing prosperity. Thus, our Chinese name, "華城" (FORTUNE), and our English name, "FORTUNE" (幸福), were carefully chosen to harmonize both in sound and meaning. To help our friends and supporters gain a deeper understanding of FORTUNE, we have outlined some of our core philosophies and visions below. We welcome your encouragement and guidance.
1. FORTUNE Spirit
"Develop high-quality products that benefit human life, supplying them to society in sufficient quantities and at reasonable prices to improve human society." "Generate profits, enhance employee welfare, pursue happiness, work together in harmony, and share prosperity and peace."
2. FORTUNE Culture
"Diligence," "Sincerity," "Perseverance," "Pursuit of Perfection and Excellence," "Customer Care," and "Giving Back to Society."
3. Business Philosophy: Quality, Participation, Well-being, Sustainability
- Quality Management: A business centered on quality, ensuring excellent products and services through high operational standards.
- Participatory Management: Full employee involvement, where employees are also shareholders; fostering internal entrepreneurship, workplace harmony, environmental balance, and social welfare.
- Well-being Management: Generating profits to benefit employees, customers, shareholders, and partner suppliers; creating a welfare-oriented FORTUNE, and producing high-quality, reasonably priced products to contribute to society.
- Sustainable Operation: Continuously developing new products and exploring new markets, striving together for the ideals of FORTUNE, ensuring that all operations today create a better tomorrow.
4. Quality Policy: Customer Care, Adherence to Six Sigma (6σ)
- Customer First – Oriented towards customer satisfaction.
- Full Participation – Involvement of all employees, regardless of hierarchy.
- Process-Oriented – Enhancing efficiency through the PDCA (Plan-Do-Check-Act) cycle.
- Continuous Improvement – Managing with Six Sigma (6σ) as the goal.
- Profit Generation for Well-being – Mutual prosperity and sustainable welfare.
5. Environmental Policy
- Commitment to Reducing and Preventing Pollution Emissions.
- Continuous Implementation of Waste Reduction.
- Fostering Environmental Awareness Among All Employees and Conserving Resources.
- Commitment to Complying with Environmental Regulations and Continuous Improvement.
6. Energy Policy
FORTUNE Electric Co., Ltd., based on corporate social responsibility and sustainable operation goals, collectively implements the ISO 50001:2011 Energy Management System with all employees.
Our Commitment to Energy Policy:
Enhancing Energy Efficiency and Continuously Improving Energy Performance.
Complying with Energy-Related Regulations and Prioritizing the Procurement of Energy-Efficient Products.
Reviewing Energy Targets to Ensure Access to Information and Resources.
Implementing the Energy Management System with Full Employee Participation in Energy Conservation and Carbon Reduction.
Creating Corporate Energy Value and Establishing a Sustainable Corporate Culture.
7. Occupational Safety and Health Policy: Compliance, Prevention, Continuous, Co-Protection
- Compliance (Compliance with Regulations): Adhere to environmental protection, occupational health and safety, fire safety, and other relevant regulatory requirements and superior orders. Regular inspections are conducted to ensure that the surrounding area of the factory complies with safety and health standards.
- Prevention (Hazard Prevention): Based on the annual workplace injury report, the risks associated with crane operations, working at heights, and commuting accidents are identified as key management priorities. Hazard prevention and process improvement are the primary approaches, with strict material selection during the development phase and proactive efforts to find alternative materials. Automatic inspections are implemented to enhance work efficiency and reduce potential safety and health impacts from various products, activities, and services.
- Continuous Improvement: By utilizing the PDCA cycle and proposal improvement systems, the factory continually implements audit activities and management reviews to meet the requirements of safety and health policies, objectives, and management programs. This approach aims to enhance the factory's self-management capabilities in safety and health.
- Co-Protection (Self-care and Caring for Others): Actively participate in safety and health activities, providing safety awareness and training to employees and contractors. Establish internal consensus and maintain good communication channels, ensuring that all stakeholders work together to improve safety and health.。
8. Risk Management Policy
- Creating Company Value: Maximizing customer and investor benefits while aligning with the company's operational strategy, preventing potential risks, and achieving a balance between risk and return to generate profits and well-being.
- Pursuing Corporate Sustainability: Establishing and implementing a risk management system to effectively identify, analyze, assess, and address risks associated with business operations. Continuously monitoring and reviewing its effectiveness ensures that risks remain within acceptable tolerance levels for stakeholders, fulfilling the company's mission of sustainable operation.
- Comprehensive Risk Management: A top-down approach, driven by company commitment and the establishment of risk management mechanisms, enhances employees' risk awareness. A bottom-up approach, through education and training, cultivates employees' risk management capabilities, shaping a corporate risk management culture. This ensures that risk management is effectively integrated into company policies and embedded in employees' daily work and lives.
9. Human Resources Policy and Commitment
Integrating Group Resources and Strengthening Competitive Advantage.
Cultivating Core Competencies and Enhancing Technical Expertise.
Implementing Clear Responsibilities and Emphasizing Full Employee Participation.
Developing Top-Tier Talent and Advancing Towards Sustainable Operations.
10. Information Security Policy
Implement information security and strengthen service quality
Strengthen risk management to ensure continuous operation
Prepare for emergencies and ensure rapid disaster recovery
Reasonable use of personal data and prevention of data leakage
11. Long-Term Business Strategy
Committed to technology and specialization, institutionalization, diversification, and internationalization, striving to make FORTUNE the leading heavy electrical machinery manufacturer in the country.
12. Vision and Core Values of FORTUNE Electric
Vision of FORTUNE Electric: To become a world-class electrical machinery company.
Since its founding in 1969, FORTUNE Electric has upheld the FORTUNE Spirit of "Diligence, Sincerity, Pragmatism, and the Pursuit of Excellence." Through ethical management, unity, and dedication, we have strived for excellence in the heavy electrical machinery industry, earning the trust and recognition of our customers while achieving steady annual growth.
Moving forward, we will distinguish our services through "Pre-Sales and After-Sales Support" and "Emergency Power Restoration Services." We will continue to develop and innovate new products and technologies, elevating the traditional heavy electrical industry into a high-tech sector.
By actively expanding product exports and pursuing international investment strategies, we aim to become the leading heavy electrical manufacturer in the country and a globally recognized electrical machinery company.
Core Values of FORTUNE Electric:Innovation, R&D, Quality, Participation, Well-being, and Sustainability.
Quality-Centered Management: The quality of products, services, and people is the lifeblood of the company.
Encouraging Innovation and Pursuing Excellence: A healthy mindset fosters creativity, and innovation drives FORTUNE's success—never settling for the status quo.
Fulfilling Corporate Social Responsibility: Moving from individual well-being to collective prosperity—harmonizing with the environment and excelling in our work is a direct way to contribute to society and the power industry.
Mission of FORTUNE Electric:Security for Employees, Security for Customers, Security for Shareholders, and Security for Society.
Generating Profit and Well-being through Technology and Management:Utilizing technology to create profit and well-being for employees, customers, partners, and shareholders, while contributing to the greater welfare of humanity.
Business Goals of FORTUNE Electric/p>
- ◎Develop high value-added and eco-friendly energy-saving products.
Enhance product cost-efficiency and reliability to create added value. - ◎Strengthen turnkey project capabilities.
Enhance full-system supply capability through turnkey project execution. - ◎Reduce costs and enhance competitiveness.
Reduce procurement and manufacturing costs through design standardization, optimization, Just-In-Time (JIT) production, and Total Productive Maintenance (TPM) system management.
- ◎Enhance operational and management efficiency.
Integrate information and management systems with an efficiency-oriented approach to enhance corporate operations. - ◎Expand into the electrical machinery sector.
Leverage the foundation of the heavy electrical industry to expand into related electrical machinery sectors. - ◎Optimize global production and sales operations.
Optimize global production capacity based on sales plans and implement accordingly.
- ◎Establish global strategic Original Design Manufacturing (ODM) partnerships.
Leverage resources from technical partner manufacturers to undertake product manufacturing. - ◎Diversified Business Operations.
Expand into related industries based on the electrical machinery sector to diversify business risks. - ◎Establish a Corporate Group.
Transform into a corporate group, leveraging integration and specialization to maximize overall competitiveness.